Importance Of High Quality Warping Machines
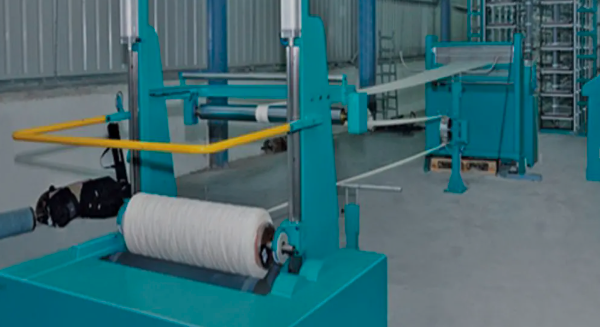
In the realm of textile manufacturing, the significance of high-quality warping machines cannot be overstated. Warping is a crucial process that lays the foundation for subsequent weaving and knitting processes in the production of fabrics. The evolution of warping technology has played a pivotal role in enhancing efficiency, precision, and overall productivity in the textile industry. This article delves into the multifaceted importance of employing advanced warping machines, exploring their impact on production, quality, and the industry as a whole.
1. Precision and Consistency: The Cornerstones of Quality
1.1 Precision Engineering
High-quality warping machines are engineered with precision in mind. These machines ensure the accurate alignment of warp yarns, minimizing variations in tension and length. Precision in warping is indispensable for producing fabrics with uniform patterns and textures, meeting the stringent quality standards demanded by modern consumers.
1.2 Consistent Output
Consistency in warp yarn tension and length directly translates to consistent output in the weaving and knitting processes. A deviation in yarn parameters can result in defective fabrics, affecting the overall quality of the end product. High-quality warping machines act as guardians of consistency, paving the way for a seamless downstream manufacturing process.
2. Increased Productivity and Efficiency
2.1 Rapid Warping Speeds
Modern warping machines boast impressive speeds, significantly reducing the time required for the warping process. This increase in efficiency directly contributes to higher overall productivity in textile manufacturing. Manufacturers can meet demanding production schedules and capitalize on market opportunities with the aid of these high-speed machines.
2.2 Reduced Downtime
Reliability is a hallmark of high-quality warping machines. With advanced features and robust design, these machines experience minimal downtime, ensuring continuous production. The reduction in downtime not only enhances efficiency but also minimizes production costs, making the manufacturing process economically viable.
3. Adaptability to Diverse Yarn Types and Fabrics
3.1 Versatility in Yarn Handling
The textile industry thrives on diversity, with an array of yarn types and fabric specifications. High-quality warping machines exhibit versatility in handling various yarn types, including natural fibers, synthetic yarns, and blends. This adaptability empowers manufacturers to explore innovative textile creations, meeting the dynamic demands of the market.
3.2 Customization Capabilities
Customization has become a key driver in the textile industry, with consumers seeking unique and personalized products. Advanced warping machines facilitate customization by allowing manufacturers to experiment with different yarn combinations and fabric structures. This adaptability positions manufacturers to cater to niche markets and stay ahead in the competitive landscape.
4. Technological Advancements and Industry 4.0 Integration
4.1 Automation and Digitalization
High-quality warping machines are at the forefront of technological advancements, embracing automation and digitalization. Automated features streamline the warping process, reducing manual intervention and the risk of errors. Integration with Industry 4.0 technologies enables real-time monitoring, predictive maintenance, and data-driven decision-making, ushering in a new era of smart manufacturing.
4.2 Sustainability Initiatives
In response to global concerns about sustainability, modern warping machines incorporate eco-friendly features. Energy-efficient operation, waste reduction, and responsible resource utilization are integral aspects of these machines. Manufacturers adopting high-quality warping machines not only benefit from enhanced efficiency but also contribute to the industry’s efforts toward sustainability.
5. Quality Assurance and Cost Management
5.1 Minimized Yarn Breakages
Yarn breakages during the warping process can lead to production delays and increased waste. High-quality warping machines are designed to minimize yarn breakages, ensuring a smooth and uninterrupted workflow. This reliability directly influences production timelines and cost management.
5.2 Long-Term Cost Savings
While the initial investment in high-quality warping machines may seem significant, the long-term cost savings are substantial. The durability, efficiency, and reduced maintenance requirements of these machines contribute to a favorable cost-benefit ratio over their lifespan, making them a strategic investment for textile manufacturers.
Conclusion
In conclusion, the importance of high-quality warping machines in the textile industry cannot be emphasized enough. These machines serve as the backbone of efficient and quality-driven textile manufacturing processes. From precision engineering to technological integration, the impact of advanced warping machines resonates across the entire production cycle. Manufacturers embracing these machines position themselves for success in a rapidly evolving industry, where quality, efficiency, and adaptability are the keys to sustained growth.