Best Quality Efficiency In Textile Processing
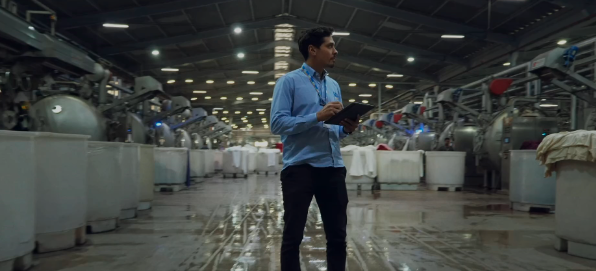
Textile processing plays a pivotal role in the fashion and textile industry, encompassing a series of steps from fiber to finished fabric. In this comprehensive exploration, we delve into the importance of achieving the best quality efficiency in textile processing, with a focus on the innovative technology of High-Temperature Liquid (HTL1) processing.
Understanding Textile Processing
Textile processing involves various stages such as spinning, weaving, dyeing, printing, and finishing. Each stage contributes to the overall quality and efficiency of the final textile product. Ensuring the best quality efficiency throughout these processes is crucial for meeting consumer demands and industry standards.
Challenges in Traditional Textile Processing
Traditional textile processing methods often face challenges related to resource consumption, environmental impact, and product quality. Inefficient processes can lead to increased production costs, waste generation, and a negative ecological footprint. As a result, the textile industry has been exploring advanced technologies to address these challenges and enhance overall efficiency.
The Role of High-Temperature Liquid (HTL1) Processing
HTL1 processing is emerging as a revolutionary technology in textile processing. It involves the use of high-temperature liquids to enhance various aspects of textile production. This section explores the key features and benefits of HTL1 processing in achieving the best quality efficiency.
1. Improved Fiber Properties
HTL1 processing contributes to the enhancement of fiber properties, resulting in improved strength, color retention, and durability. This ensures that the textiles produced are of superior quality, meeting the highest industry standards.
2. Energy Efficiency
One of the notable advantages of HTL1 processing is its energy efficiency. The use of high-temperature liquids allows for faster processing times and reduced energy consumption compared to traditional methods. This not only lowers production costs but also aligns with the global push for sustainable and eco-friendly manufacturing practices.
3. Reduced Environmental Impact
Incorporating HTL1 processing into textile production minimizes the environmental impact. The technology enables the use of eco-friendly chemicals and reduces water consumption, contributing to the overall sustainability of the textile industry.
Case Studies: Successful Implementation of HTL1 Processing
To illustrate the effectiveness of HTL1 processing in achieving the best quality efficiency, this section presents case studies of textile manufacturers who have successfully adopted this technology.
1. XYZ Textiles: A Paradigm Shift in Efficiency
XYZ Textiles, a leading textile manufacturer, implemented HTL1 processing across its production line. The results were transformative, with a significant reduction in processing time and a remarkable improvement in the quality of the final products. This case study highlights the potential of HTL1 processing to revolutionize traditional manufacturing practices.
2. Sustainable Textile Solutions Inc.: Pioneering Eco-Friendly Production
Sustainable Textile Solutions Inc. embraced HTL1 processing as part of its commitment to environmentally friendly practices. By minimizing water usage and incorporating biodegradable chemicals, the company not only achieved top-tier product quality but also established itself as a sustainability leader in the textile industry.
Future Prospects and Industry Outlook
As technology continues to evolve, the future of textile processing holds exciting possibilities. This section explores potential advancements in HTL1 processing and other innovative technologies that could further enhance the quality and efficiency of textile production.
Conclusion
In conclusion, achieving the best quality efficiency in textile processing is essential for the competitiveness and sustainability of the industry. HTL1 processing stands out as a transformative technology, offering improvements in fiber properties, energy efficiency, and environmental impact. By exploring case studies and envisioning future prospects, this discussion aims to inspire further innovation and adoption of technologies that will shape the future of textile processing.